یکی از علومی که بیشترین کاربرد را در صنایع مختلف به خود اختصاص داده, علم هیدرولیک است. البته علوم دیگری نظیر شیمی, مکانیک سیالات و ترمودینامیک نیز به کمک این علم آمده و تلفیقی از آنها را به صورت ساده در یک سیستم هیدرولیک می توان مشاهده کرد.
از طرفی با توجه به نقش اساسی و مهم سیال هیدرولیک (انتقال نیرو), بحث آلایندگی آن از اهمیت بسیار زیادی برخوردار است. در یک سیستم هیدرولیک, سیال هیدرولیک با تغییر جهت نیرو و همچنین تغییر مقدار آن باعث حذف یک سری از عملیات مکانیکی در سیستم می شود که بعنوان مثال از حذف استفاده از دنده ها, اهرم ها و نیز حذف تنش های شدید اجزای می توان سیستم نام برد. همچنین سیال هیدرولیک به دلیل انتقال سریع نیرو و تا فاصله زیاد, در شرایط دما و فشار بالا بازدهی بهتری خواهد داشت.
براساس نظر کارشناسان تعمیرات و نگهداری, حدود80 درصد خرابی ها در سیستم هیدرولیک, نتیجه مستقیم آلودگی سیال آن است. بنابراین با انتخاب یک سیال مناسب و همچنین کنترل آلاینده ها می توان آسیب های ناشی از آلاینده ها را به حداقل رساند. در این مقاله آلاینده های سیستم هیدرولیک به طور اجمالی معرفی شده و هر کدام به صورت جداگانه بررسی می شود.
حرارت بیش از اندازه (Over Heat)
متاسفانه در بسیاری از موارد, حرارت به عنوان یک آلاینده در نظر گرفته نمی شود. یکی از عوامل بوجود آمدن حرارت بیش از اندازه در سیستم می تواند مربوط به انتخاب نادرست گرید (ISO VG) روغن هیدرولیک باشد. بدین ترتیب که چون در شرایط روانکاری هیدرو دینامیک تنها اصطکاک موجود, اصطکاک داخلی روغن در گردش است, اگر گرید مصرفی بیش از گرید توصیه شده باشد به دلیل افزایش اصطکاک داخلی, دمای روغن به شدت افزایش می یابد. بر اثر افزایش غیرعادی دمای روغن, روند اکسیداسیون از حالت تدریجی خارج شده و روغن پایه به سرعت اکسید
می شود. (پس از شروع اکسیداسیون به ازای هر15 درجه سانتیگراد افزایش دما, شدت اکسیداسیون, دو برابر می شود) نتیجه این امر کاهش ادتیوهای آنتی اکسیدان و در نهایت کاهش عمر مفید روغن خواهد بود.
از دلایل دیگر Over Heat می توان به انجام تماس فلز با فلز در اثر وجود اشکال فنی در سیستم و برقراری شرایط روانکاری مرزی اشاره کرد که باعث سایش مکانیکی قطعات می شود. در برخی موارد نیز بدلیل طراحی نامناسب, انتقال حرارت موثر بین سیستم و محیط انجام نشده و در شرایط آب و هوایی گرم, تاثیر پذیری سیستم از محیط بسیار زیاد می شود.
در نهایت با افزایش عدد اسیدی و تحلیل ادتیوها در روغن, میزان خوردگی و زنگ زدگی قطعات نیز افزایش می یابد. از طرف دیگر بدلیل افزایش گرانروی روغن (اکسیداسیون) جریان روغن درون سیستم کاهش یافته و بدلیل افت فشار, دقت کنترل سیستم کاهش خواهد یافت.
برای رفع چنین مشکلاتی در سیستم می توان ضمن انتخاب صحیح گرید سیال هیدرولیک و نیز اطمینان از طراحی مناسب, با افزایش ظرفیت تغذیه روغن و همچنین افزایش سرعت گردش آن, دمای روغن را در حد مطلوب کنترل کرد که بنا به عقیده کارشناسان تعمیرات دمای روغن در مخزن اصلی هیدرولیک, نباید از60 درجه سانتیگراد تجاوز کند.
آلایندگی ذرات جامد (Solid Particle Contamination)
در یک سیستم هیدرولیک بدلیل اینکه امکان حذف کامل ذرات جامد از سیال هیدرولیک وجود ندارد, بناچار برای آلایندگی ناشی از ذرات, یک محدوده تعریف می شود. در سیستم های امروزی که دارای لقی مجاز (Clearance) بسیار کمی بوده و در فشارهای به نسبت بالا (بیشتر از 7 bar ) کار می کنند کنترل آلاینده های جامد از اهمیت بسیار زیادی برخوردار است. منابع ورود ذرات جامد به سیستم می تواند از طریق هوای ورودی به سیستم از محیط (گرد و غبار), ذرات عبوری از آب بندها, باقی ماندن ذرات درون سیستم هنگام نصب قطعات و نیز ذرات حاصل از سایش داخلی قطعات باشد. حضور این ذرات در سیستم می تواند سبب بوجود آمدن صدمات مکانیکی (پارگی شیلنگها و شکستن Valve ها), سایش و خراشیدگی سطوح فلزی, گرفتگی فیلترها و در نهایت ایجاد افت فشار در سیستم شود که نتیجه این امر کاهش میزان تولید و افزایش هزینه های کلی تعمیرات خواهد بود.
برای جلوگیری از ورود ذرات به سیستم, باید تمامی سیالات, قبل از ورود به مخزن, فیلتر شده و در نواحی قرارگیری سیستم در معرض هوای محیط, فیلترهای مناسب بکارگرفته شوند. هم چنین فلاشینگ نهایی سیستم پس از نصب قطعات (قبل از راه اندازی) و نیز بازرسی شرایط آب بندها و درپوش مخازن مرکزی می تواند مانع ورود ذرات جامد به سیستم شود. از طرفی بررسی فیلترها از نظر مش صحیح ( اندازه منافذ و تعداد) و جنس آنها با توجه به نوع عملیات, می تواند بازدهی فیلتراسیون را در سیستم افزایش داده و با در نظر گرفتن لقی مجاز قطعات می توان محدوده مناسبی برای آلاینده ها تعریف کرد.
یکی از روشهای اندازه گیری, روش اسپکتروسکوپی است که بدلیل محدودیت این روش (عدم اندازه گیری ذرات بزرگتر از7 میکرون), روش های دیگری نظیر NAS و اخیراً روش ISO 4406 بکار گرفته می شوند.
در این روشها, با توجه به لقی مجاز قطعات و توصیه سازنده اصلی تجهیزات (OEM) یک محدوده بعنوان کد تمیزی سیستم در نظر گرفته می شود, بدین ترتیب که بوسیله شمارش الکترونیکی ذرات با توجه به سایز آنها (در محدوده بین5,2 تا15 میکرون) کد تمیزی سیستم مشخص می شود. بعنوان مثال سازنده ویکرز برای یک سیستم هیدرولیک
کد ISO 4406 18/16/13 معادل با NAS 1638 Level 7 را بعنوان کد تمیزی سیستم در نظر گرفته است که اگر میزان آلاینده ها از این حد تجاوز کند, با بهبود فیلتراسیون ( یا تعویض فیلتر) و در صورت لزوم جایگزینی روغن جدید می توان آثار مخرب آلاینده ها را به حداقل رساند.
آلایندگی آب (Water Contamination) :
میزان ایده آل آب در یک سیال هیدرولیک, کمتر از میزان اشباع آن (در دمای عملیاتی دستگاه) است. حدود (200-300)ppm آب می تواند بصورت محلول در سیال پایه معدنی وجود داشته باشد بدون اینکه رنگ روغن تغییر کند.
اگر میزان آب به 500 ppm افزایش یابد, روغن کمی کدر شده و به اصطلاح ظاهر آن ابری می شود. بالاترین میزان مجاز آب در یک سیال هیدرولیک 100 ppm بوده و اگرمیزان آب از 0.1 درصد وزنی تجاوز کند, بصورت آب آزاد ظاهر خواهد شد. آب بدلیل کاهش مقاومت فیلم روانکار باعث افزایش شدت سایش شده و در حضور فلزاتی نظیر مس, شدت سایش دو برابر خواهد شد.
از طرفی بدلیل کاهش ادتیوهای R&O , میزان خوردگی و زنگ زدگی سطوح فلزی افزایش یافته و در حضور کاتالیزورهای فلزی, تخریب سطوح چند برابر می شود. همچنین بدلیل انجام سریع اکسیداسیون, لجن اسیدی در سیستم ایجاد شده و راندمان فیلتراسیون کاهش می یابد.
بهترین روش برای اندازه گیری میزان آب, آزمایش کارل فیشر است. برای جلوگیری از ورود آب به سیستم می توان به مواردی نظیر دقت در انبارداری صحیح, برطرف کردن نشتی از مبدلهای حرارتی یا ورودی های مخزن و تعویض آب بندهای آسیب دیده, اشاره کرد.
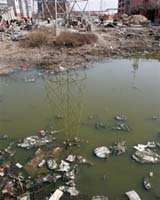
آلایندگی هوا (Air Contamination) :
یکی دیگر از آلاینده هایی که در ارتباط با سیال هیدرولیک می توان به آن پرداخت, حبابهای هواست. خروج حبابهای درون سیال در مواقعی که فشار اعمال شده روی سیال از فشار اشباع حلالیت هوا در آن کمتر باشد, می تواند با شکستن و از بین رفتن ناگهانی باعث بروز حوادثی نظیر کاویتاسیون شود. یکی دیگر از صدماتی که حضور حبابهای هوا درون روغن هیدرولیک ایجاد می کند, تولید کف (تراکم پذیر) و افزایش شدید درجه حرارت بدلیل کاهش حجم درون سیلندر هیدرولیک است که این افزایش دمای ناگهانی باعث تسریع روند اکسیداسیون خواهد شد.
برای جلوگیری از ورود هوا به سیستم می توان با تامین هد مورد نیاز پمپ از بوجود آمدن افت فشار در اریفیس ها و همچنین مقاومت در مکش و هواگیری پمپ ها جلوگیری کرد.
در برخی موارد باز و بسته شدن سریع شیر کنترل ها (ایجاد توربولنسی), تنفس کلاهک مخزن و ورودی های سیستم می تواند بعنوان منابع ورود هوا به سیستم باشند که با رفع این عیوب, تشکیل حبابهای هوا در سیال هیدرولیک به پایین ترین میزان ممکن خواهد رسید.

مشکل نشتی (Leakage)
متاسفانه در جامعه صنعتی, نشتی بعنوان یک امر معمولی در نظر گرفته شده و برای رفع آن, تلاش جدی صورت نمی گیرد. بررسی آثار نامطلوب نشتی در یک سیستم می تواند اهمیت آنرا بیش از پیش مشخص ساخته و تاثیر آن را در کیفیت محصول نهایی و افزایش هزینه های تمام شده, نشان دهد.
در یک سیستم هیدرولیک بدلیل نشتی, همواره میزان مصرف روغن از ظرفیت واقعی مخزن بیشتر بوده و هزینه های مربوط به خرید روانکار افزایش می یابد. از طرفی بدلیل کاهش جریان روغن و ایجاد افت فشار, دقت کنترلی سیستم کاهش یافته و بعلت کارکرد نامنظم سیستم, مشخصات محصول نهایی (مثلاً ابعاد) بر موارد از پیش تعیین شده منطبق نخواهدبود. در ارتباط با معضل نشتی در کنار آثار مخرب زیست محیطی (ورود روغن به منابع آب و خاک), احتمال قرار گرفتن روغن در معرض سطوح داغ (دستگاههای دایکاست و تزریق پلاستیک) و اشتعال آن وجود داشته و بروز حوادثی نظیر آتش سوزی محتمل خواهد بود.
نکته بسیار مهم دیگر در ارتباط با نشتی این است که تمامی آلاینده های یاد شده می توانند از محل نشت روغن وارد سیستم شده و استهلاک زودرس تجهیزات و ماشین آلات را باعث شوند. بنابراین بازرسی منظم اتصالات و آب بندها و تعویض آنها در صورت لزوم می تواند در کارکرد مطمئن ماشین آلات, موثر باشد.
یکی دیگر از روشهای جلوگیری از نشتی, بحث سازگاری سیال هیدرولیک با الاستومرها و انتخاب مناسب سیال هیدرولیک از نظر نقطه آنیلین است.
بدین معنی که نقطه آنیلین معرف میزان ترکیبات آروماتیک در روغن بوده و اگر از میزان توصیه شده بیشتر باشد, باعث تورم آب بندها شده و اگر کمتر از حد مجاز باشد سبب سفت شدن اتصالات و کاهش حجم آنها می شود.
از روش های موثر دیگر جلوگیری از نشتی, انتخاب صحیح آب بندها (از نظر دما, فشار و شدت جریان), تنظیم دمای سیال هیدرولیک (حداقل نگه داشتن دمای سیال) و بالانس مکانیکی سیستم (در یک راستا قرار گرفتن شفت پمپ و موتور) است که با اجرای این روشها می توان میزان نشتی را به حداقل رساند.
منابع:
- National Tribology Service (NAS)
- Oil Analysis & Lubrication Learning Center
- Hydraulic Oil Filtration System-Filtroil
- Practical Ways To Control Hydraulic System Contamination
- Lube- Tech Magazine
موضوع مطلب :